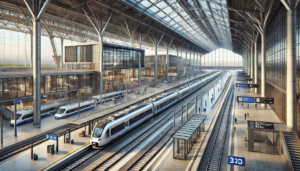
Cost estimation and optimization in the building and public works sector

In the construction and public works sector, cost estimation is a strategic issue. A miscalculation can lead to cost overruns, unexpected delays, and a loss of competitiveness in the market. Traditionally, construction companies rely on manual methods, price schedules, historical databases, or the expertise of construction economists. While these approaches are widely used, they have certain limitations, particularly in terms of responsiveness, reliability, and adaptability to market fluctuations, and they can be quite time-consuming.
The limitations of traditional costing methods
Construction companies generally use:
-
Historical databases and price schedules: While practical, these databases may not reflect recent changes in the costs of materials, equipment, and labor.
-
Spreadsheet software: Often developed in-house, these tools are prone to human error and require regular updates.
-
The experience of economists and experts: While human expertise is valuable, it varies from person to person and is difficult to transfer to new generations.
Take the example of a structural works company estimating the costs of a commercial building project. If it relies solely on previous estimates and last year’s supplier prices (DGPF), it risks facing significant discrepancies due to rising material costs and evolving regulatory requirements for sustainable construction. A poor estimation can lead to unexpected financial gaps and profitability challenges.
The contribution of data analytics and artificial intelligence solutions
To address these challenges, new data-driven and artificial intelligence-based approaches significantly enhance the accuracy and speed of cost estimation. These solutions also improve the analysis of DGPF and help identify inconsistencies in pricing. These tools leverage dynamic and up-to-date databases, combined with machine learning algorithms.
Key benefits of a modern costing solution
-
Reduction in analysis time
Unlike traditional methods that require several days of study, a data-driven tool can provide estimates in just seconds, optimizing feasibility study time and enabling much faster budget assessments.
-
Improved accuracy
The integration of real-time data accounts for market fluctuations, minimizing discrepancies between forecasts and actual costs.
-
Standardization and reliability of cost estimations
A unified methodology reduces estimation discrepancies between different experts, ensuring greater consistency in evaluating technical lots and equipment.
-
Identification of optimization opportunities
A predictive analytics approach helps identify optimization levers (choice of materials, alternative suppliers, installation solutions, etc.) and focus on key cost drivers.
-
Cost savings in supplier/contractor negotiations
Analytics and AI-based solutions help detect inconsistencies in supplier/contractor pricing (DGPF), allowing for better negotiation leverage.
-
Better knowledge management and cross-team collaboration
AI-processed data is collected and enables better capitalization on essential project data. Collaboration among different teams (Estimating, Program Management, Procurement, etc.) is thereby strengthened.
A real-world example illustrates this transformation: A finishing works company specializing in installing technical equipment (HVAC, electricity, plumbing) improved its quoting accuracy by 20% after integrating an advanced analytics solution, reducing gaps between budget forecasts and actual project costs.
Towards more reliable and adaptive cost estimation
The evolution of estimation tools in the construction industry now allows companies to overcome the limitations of traditional approaches. Adopting advanced analytical methods is no longer a luxury but a necessity to remain competitive in an ever-changing environment.
Companies in the sector should explore these new solutions to secure their projects and better control their costs. In the long run, improved cost management can contribute to more efficient planning and resource optimization—key elements to ensuring profitability and the long-term viability of construction projects.
All articles
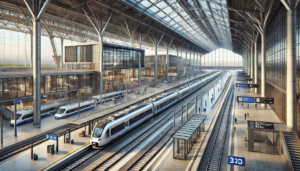
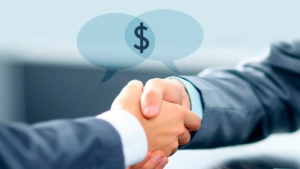
